Wechselrichter und Umrichter
DC-AC converter (DC-AC)
• This type of converter converts direct current into alternating current.
• Often referred to as an inverter, used in applications such as solar installations to convert the direct current generated by solar panels into the alternating current required by the grid.
AC to DC converter (AC-DC)
• Converts alternating current to direct current, often as a rectifier
• Used in chargers for electronic devices or to supply DC systems.
Frequency inverter (Variable Frequency Drive, VFD)
• A special type of converter that controls the frequency and voltage of the alternating current.
• Often used in drive technology to operate electric motors more efficiently by adjusting their speed and power.
Voltage converter (DC-DC converter)
• This type of converter converts a DC voltage into another DC voltage, either at a higher or lower voltage level.
• Used in many electronic devices to adjust the required operating voltage.
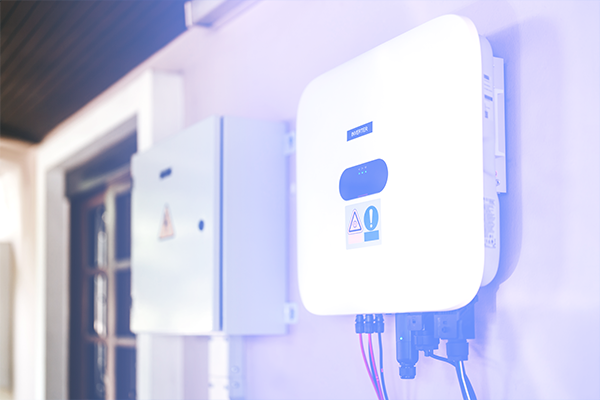
Applications of converters
Inverters are widely used in various fields, such as:
• Solar and wind energy plants: In addition to the conversion of direct current from solar modules into usable alternating current for households or the grid, we also supply cooling systems for inverters and converters in wind turbines.
• E-mobility: converters control and optimise the flow of electricity in electric vehicles.
• Industrial applications: Frequency converters are used in industry to control the motors in machines and production plants.
• Household appliances and electronics: Converters are found in many household appliances that need to adjust power to different voltage levels.
In summary, the inverter is a central device in power electronics that makes it possible to efficiently convert electrical energy and to change the properties of the current for specific applications.
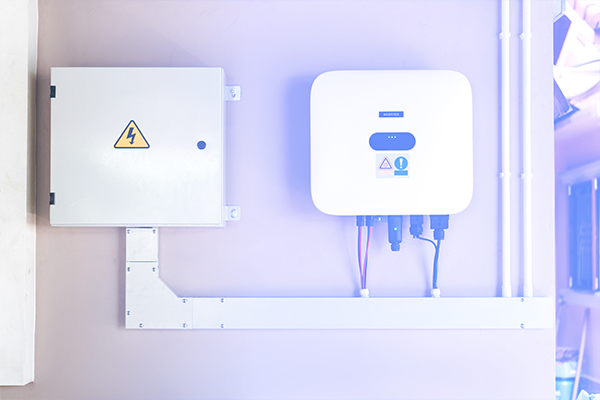
Cooling of inverters
The cooling of inverters is important for several reasons, as it directly affects the efficiency, reliability and service life of the device. Inverters generate heat during the conversion process, particularly due to losses in the circuitry and internal resistors. Insufficient cooling can lead to overheating, which affects the operation and durability of the device.
Avoidance of overheating and damage to components
• Inverters contain electronic components such as power transistors, capacitors and diodes that are sensitive to high temperatures.
• Overheating can cause permanent damage, impair the functionality of individual components and render the inverter unusable.
Ensuring stable performance and efficiency
• When an inverter overheats, it can no longer work efficiently because some components are forced to reduce their output.
• Many inverters have protective mechanisms that reduce power or shut down the device to prevent damage when they overheat. However, this affects the efficiency and functionality of the system.
Extension of the service life of the inverter
• Most electronic components have a longer lifespan when operated within a certain temperature range.
• Excessive operating temperatures accelerate the ageing of components, especially capacitors, which are frequently used in inverters. Good cooling helps to ensure that the inverter continues to work reliably for longer.
Minimize energy losses
• When an inverter overheats, the internal resistance of some components increases, which leads to higher energy losses.
• The additional losses caused by poor cooling reduce the overall energy efficiency of the system and result in more energy being lost as waste heat.
Avoidance of thermal runaway
• At very high temperatures, power semiconductors can suffer from a phenomenon known as thermal runaway. During this process, the losses increase to such an extent that the component is destroyed in a very short time.
• Effective cooling prevents the components from reaching this critical range.
safety aspects
• High temperatures inside an inverter enclosure increase the risk of fire, especially in large systems or under extreme environmental conditions.
• Cooling helps to keep the housing and the surrounding components at a safe temperature.
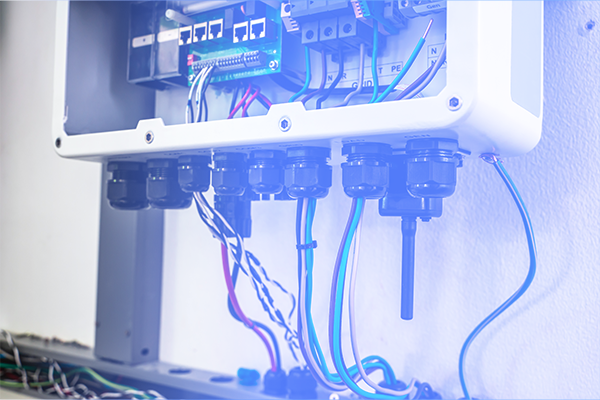
Cooling techniques for inverters
• Air cooling: fans generate an air flow and conduct the heat away from the critical components.
• Liquid cooling: For larger or more power-hungry systems, liquid cooling is used to efficiently remove heat.
• Heat sinks and heat sinks: Many inverters are equipped with heat sinks that facilitate heat dissipation to the surrounding air.
In summary, cooling an inverter is essential to maintaining performance and lifespan, preventing damage due to overheating, and ensuring safety. It is therefore a critical aspect of inverter design and operation, especially in high-power applications.
Air cooling of inverters
Flow-optimized housing design
• The inverter casing should be designed so that the air can flow through it without resistance or turbulence.
• A straight airflow path is ideal, as this ensures that the air flows evenly over the critical components and carries the heat with it.
– An air inlet on the bottom or one side and an outlet on the opposite side or at the top are effective arrangements for effectively conducting the heat generated out of the housing.
Use of high-performance fans
• Powerful fans ensure sufficient air flow, especially when the inverter is operating at high power and producing more heat.
• The fans should be arranged so that cooler air is drawn into the case from the outside and warm air is efficiently expelled to the outside.
• Intelligent control of fan speed (e.g. depending on temperature) can help to operate fans efficiently while minimising energy consumption and noise.
Targeted positioning of the heat sinks
• Heat sinks made of thermally conductive materials (e.g. aluminium or copper) are attached to the hottest components, such as power transistors and diodes, to dissipate heat quickly.
• The heat sink should be designed to have a large surface area and many fins to maximise heat exchange with the air.
• The heat sinks should be placed in the air flow of the fan so that the air flowing through them can quickly dissipate the heat absorbed by the heat sinks.
Ducting for air control
• With air ducts inside the housing, the airflow can be directed to the places that need the most cooling.
• The channels direct the air over the heat-generating components and prevent the air from ‘straying’ or flowing too quickly past heat-sensitive components.
• This targeted control helps to achieve an effective cooling effect even at lower fan speeds.
Thermal decoupling and insulation
• Heat-sensitive components such as capacitors or ICs should be mounted thermally decoupled from heat-intensive components such as power transistors.
• An insulating arrangement of the components prevents the heat from highly heated components from spreading to more temperature-sensitive components.
• This keeps the thermal load on the more sensitive parts low, which extends the overall service life of the inverter.
Use of thermal sensors and temperature monitoring
• Multiple temperature sensors in strategic positions enable continuous monitoring of heat distribution in the inverter.
• These sensors can work in conjunction with an automatic fan speed controller to dynamically adjust fan performance based on temperature load.
• A warning system or automatic shutdown at high temperatures can also be integrated to protect the inverter from overheating.
Filtering the supply air
• To prevent dust and dirt from collecting inside the inverter, air filters should be attached to the air inlets.
• Dust deposits on the heat sinks and electronic components would impede heat dissipation and reduce cooling performance.
• The filters should be cleaned or replaced regularly to ensure long-term air cooling efficiency.
• Cool air is drawn in from outside through one or more fans and directed to the components via a duct.
• The air flows along the heat sinks, which are attached to heat-generating components, and absorbs the heat from the components.
• The heated air is removed to the outside by a second fan or a natural air outlet.
Careful design and coordination of these elements allows an efficient air-cooled inverter to be realised that works reliably and at a stable temperature.
We will be happy to answer any questions you may have and look forward to hearing from you.
You can reach us Monday to Thursday from 8 a.m. to 5 p.m. and Friday from 8 a.m. to 2 p.m.